In recent times, awareness about the impacts of the textile industry has risen widely, also in the public domain, where initiatives such the Fashion Revolution global movement or Greenpeace through its Detox my Fashion campaign are strongly committed to informing the customers about the social and environmental implications the current way of producing, selling and consuming garments has. Several non-profit organisations, foremost the Ellen MacArthur Foundation, but also innovation platforms such as Fashion for Good and many more, make great efforts in analysing, understanding and indicating viable solutions in overcoming the ‘take-make-waste’ pattern the fashion industry seems to be stuck in. We have now arrived at a point where the fashion system itself recognises the need for change and embraces sustainability as the new must have.
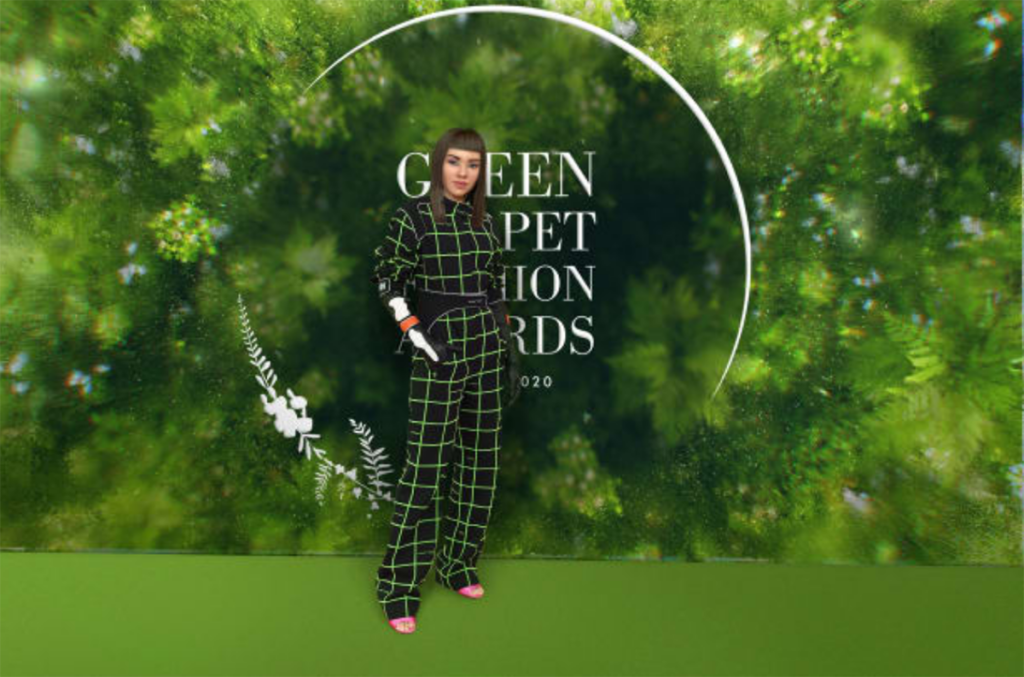
In this context, man-made cellulosic fibres (MMCF) have gained spotlight being promoted to the final consumer as a less impacting choice, especially compared to fossil-based fibres. However, cellulosic fibers are not as ‘green’ as the simple statement that they are from natural sources suggests. The starting material currently used to manufacture MMCF is bleached wood pulp, called dissolving pulp, and obtained after an additional step in the Kraft process used by paper mills. Dissolving pulp is so named because it is not made into paper, but dissolved either in a solvent or by derivatization into a homogeneous solution. Once dissolved, it can be spun into textile fibers. One approach in GRETE to tackle the sustainability issues of the MMCF production process is to define pre-treatments for the wood pulp that makes paper grade pulp – an intermediate good of paper manufacturing and recycling process – accessible as a raw material for MMCF, avoiding the energy, water and operational cost consuming dissolving grade pulps.
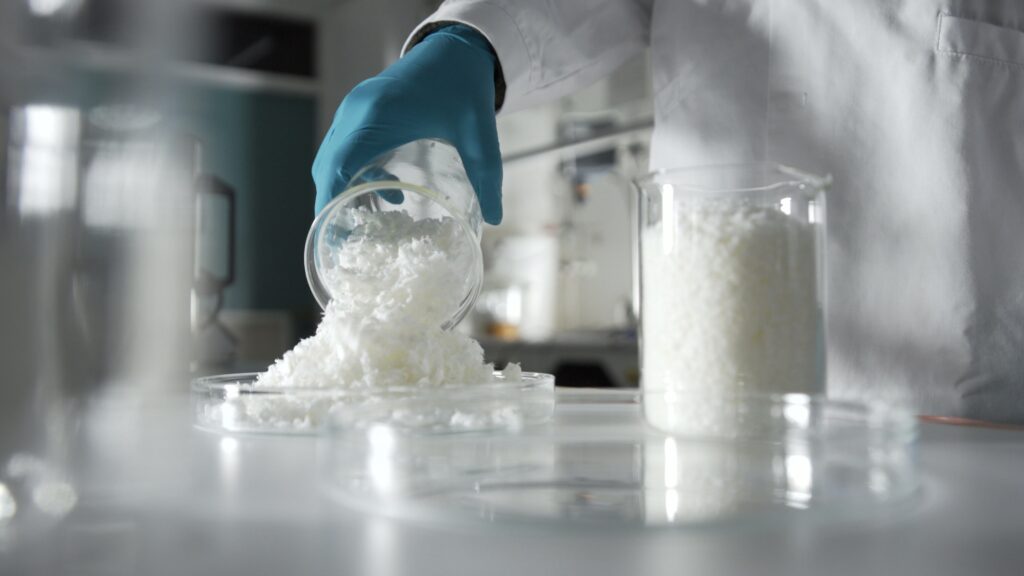
The two key processes in operation worldwide to produce MMCF are the viscose process, producing almost 90% of the world’s viscose filament and staple fibre, and the Lyocell process accounting for a further 10%. The viscose process relies on highly toxic carbon disulphide (CS2) as a solvent and although this is recovered within the process, there is the challenge of handling this material as well as discharges to the atmosphere of wastes including sulphur to air and sulphuric acid. In recent years, standards have been improved as latest technologies have been more widely implemented. Whereas, the Lyocell process uses N-methylmorpholine N-oxide (NMMO) as the solvent and, with reduced waste volumes, is seen as more environmentally friendly.
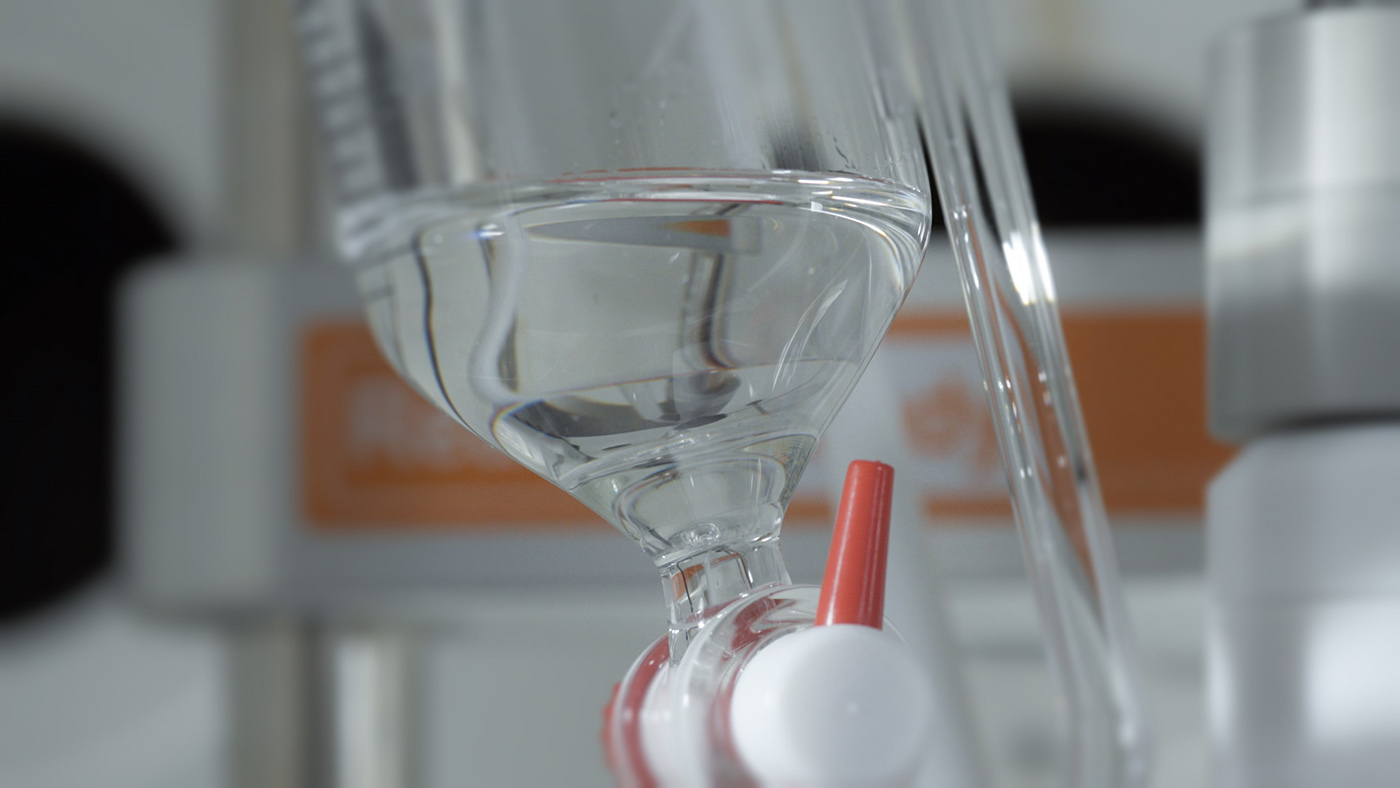
In parallel to opening up paper pulp as a more sustainable raw material, the GRETE researchers are studying Ionic Liquids to be used in the fibre spinning process. The NMMO-based Lyocell process has been studied as a benchmark for the GRETE’s Ionic Liquid-based process. The objective of the study was to create a realistic model of the Lyocell process by using the steady-state simulation software Balas® and analysing five solvent recycling concepts. The model provides data from which the accumulation of impurities in the process loops can be studied, one of the most important aspects to be solved in order to make the current linear approach more circular.
The GRETE project is the result of the consortium partners’ commitment to fundamental basic research with the goal to improve the sustainability of man-made cellulosic fibres and addressing the issues of the current solutions. Follow us on social media Facebook, LinkedIn, Instagram, Twitter and subscribe to our newsletters.